
Control methods for brushless DC and stepper motors
The Nanotec controllers and motors with integrated controller can be controlled by means of four different methods. DIP switches, configuration files, or software enable the user to select a method. Please refer to the product data sheets for supported control variants.
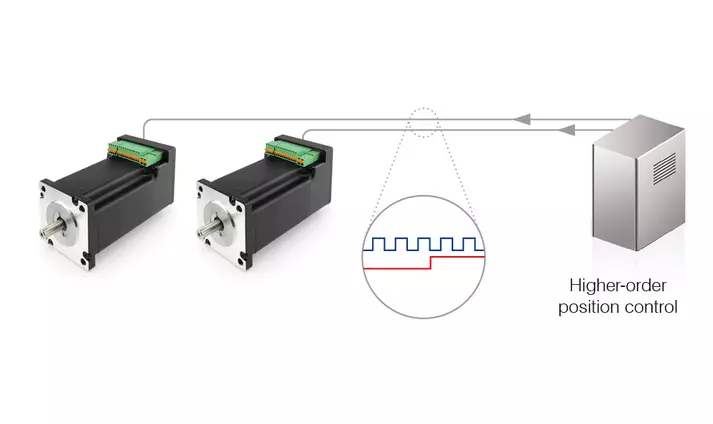
Clock & direction
In clock-direction mode, the motor is operated with a clock and direction signal via digital inputs by a higher-level positioning controller. With each clock signal, the motor moves one step in the direction given by the direction signal.
The software-based control of the Nanotec controllers enables a flexible interplay between the clock signal and position. No microstepping is required to achieve sine commutation for the motor, as the input signals are always interpolated in the background. This means that older, higher-level controllers that output only full or half steps can also benefit from the quiet running characteristics of microstepping.
The number of steps per revolution can also be specified as a rational number (numerator/denominator). By decoupling the actual step angle or number of poles of the motor, it is also easily possible to swap out the motor type in existing applications and, for example, replace a 3-phase stepper motor with a brushless DC motor, without having to change the number of cycles.
A right/left rotation mode (CW/CCW) is available in addition to the conventional clock-direction mode, in which the input used is decisive for the direction.
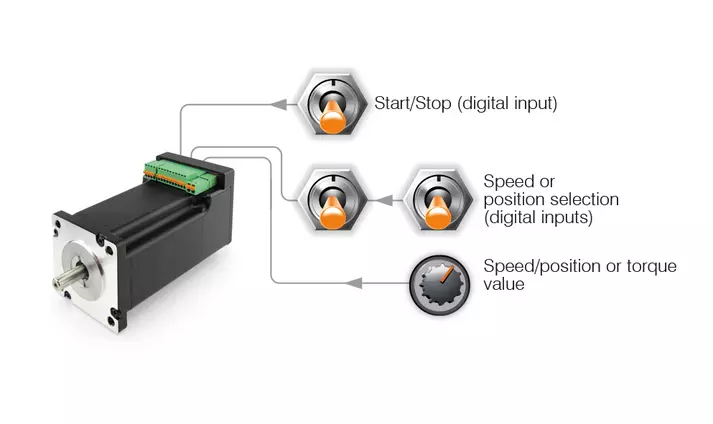
Set value setting via analog and digital inputs
The digital and analog inputs of the Nanotec controllers can be read out in milliseconds and processed in an internal sequence program. This means that, for example, the speed, position, or even the torque can be controlled via an analog input. The digital inputs can also be used to start a movement or to select different speeds, for example.
The inputs are assigned to functions via a program that uses the NanoJ V2 programming language. This program is created in Plug & Drive Studio.
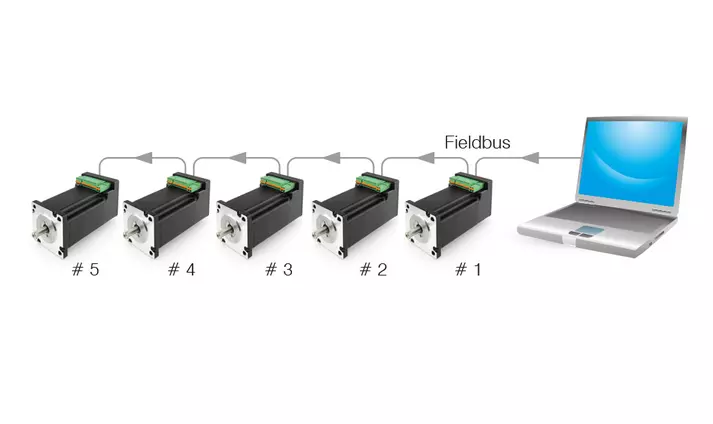
Fieldbus
The Nanotec controllers and the motors with integrated controllers can be operated via the fieldbus with a wide range of master controllers (PLCs). In this case, the controllers act as slaves that convert the commands of the higher-level controller. Nanotec offers the following fieldbus options:
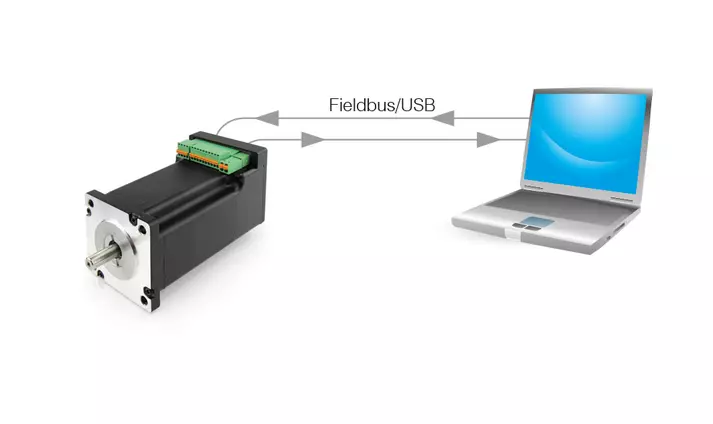
Sequence control for standalone operation or distributed intelligence
The programming environment provided in Plug & Drive Studio makes it possible to create programs in the C++ based programming language NanoJ V2. These programs run autonomously and directly on the controller or motor with integrated controller and can be saved on the controller via fieldbus or USB.
In addition to simple applications for controlling via digital/analog inputs for standalone operation, complex applications that are controlled via the fieldbus are also possible. This distributed intelligence means that the bus capacity utilization for fieldbus applications can be kept low when a large number of subscribers are connected. In addition, time-sensitive functions can be performed directly via the fieldbus without delay.
- Access to all control parameters and inputs/outputs at millisecond intervals
- Variables, branches, loops as well as logical and mathematical functions