For many years now, Nanotec Electronic GmbH & Co. KG has been sponsoring research projects in Universities, Colleges and Academies with products and expertise. The funding of a scientific project is carried out under the following conditions: It is thematically innovative, it is based on methods of scientific work and its results may have a positive impact on society.
Nanotec supports Deutschlandstipendium
Since 2011, the Deutschlandstipendium provides monthly financial support of €300 to high-achieving and committed students. Modeled after the principle of public-private partnership, businesses, foundations or private individuals sponsor young talent with a pledge of €150 per month. The Federal Government matches this amount with another €150. But there is even more: Many universities and private sponsors also support Germany Scholarship holders through concurrent mentoring programs, networking events and internships.
In our view, talented scientists are the key to Germany's economic future. This has to be supported. Therefore Nanotec Electronic is one of the sponsors of Deutschlandstipendium.
Photo: Astrid Eckert, TU Munich
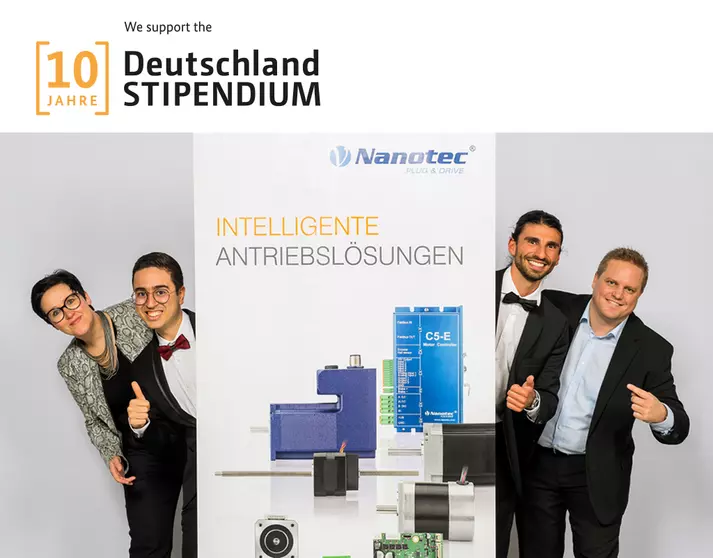
Funded projects
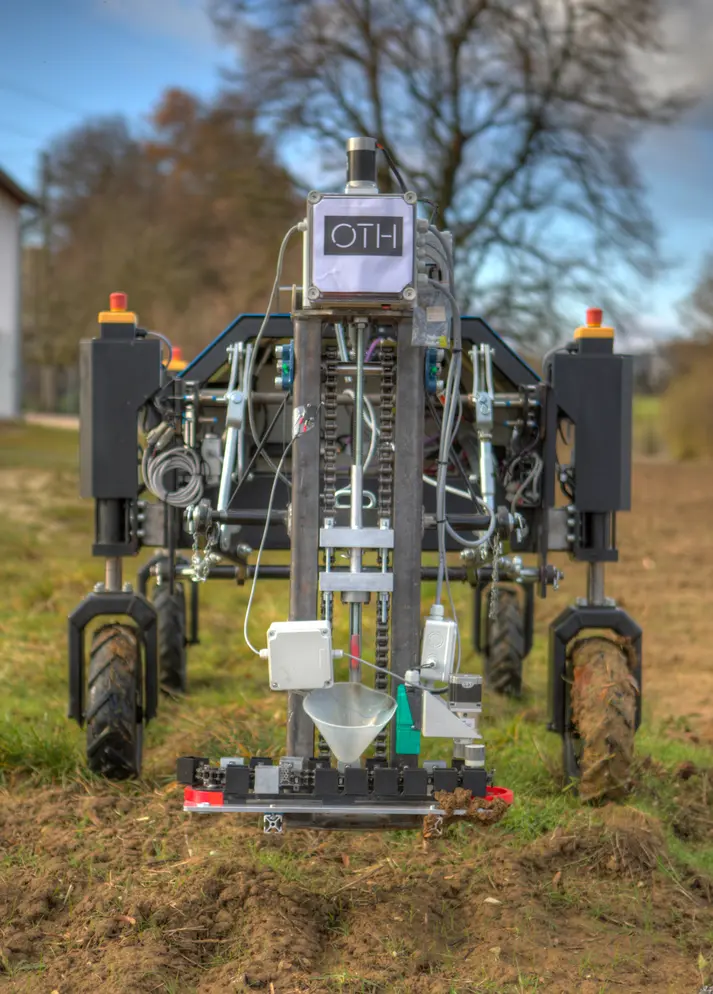
Smart soil analysis with ANELISE
The aim of the ELISE project at OTH Regensburg is to intelligently automate the analysis of soil samples. The students are focusing on optimizing the sampling process, as previous, as previous “brute force” methods often contaminate the extract, leading to incorrect measurement results.
With the help of an autonomous robot, the material is now taken more gently. ANELISE extracts the samples at predefined points, from the same depth and without adding dead microorganisms or foreign material.
Nanotec supports the project with the DB59 brushless DC motor, the GPLE40 precision planetary gearbox and the CL4 controller / drive. This package ensures precise sampling with minimal effort and offers the user real-time control of all data.
(Source and photos: Michael Fellner)
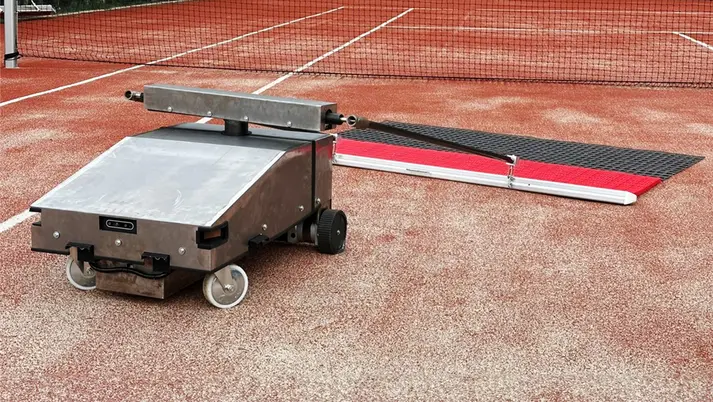
Tennis court upgrade
Students at HTL Rennweg have developed a robot that pulls a drag mat across the tennis court. At the touch of a button, the "Court Bot" moves autonomously, evenly distributing sand and smoothing out uneven spots.
To cover the entire area, the robot is equipped with zero-turn wheels. It can lift the drag mat and rotate it by 90 degrees, minimizing its work width and enabling it to navigate around obstacles, reaching every corner.
To realize this project, Nanotec provided the students with several components, including SCA5618 stepper motors, PD6 brushless DC motors with integrated controllers, and GPLE60 precision planetary gearboxes.
(Source and photos: Alexander Heim)
High-tech meets soccer
As "Delft Mercurians," students of the Robotics Student Association Delft (NL) are competing in the RoboCup. In its Small-Sized League, they face teams from around the world.
In a miniature robot soccer match, two teams of six autonomous units compete against each other. These robots must perform with precision and at high speed while complying with physical restrictions and rules similar to those of "real" soccer.
To meet these challenges, Nanotec supports the TU Delft students by providing several flat DF45 external rotor motors and high-resolution NME2 encoders. These components offer extra torque and speed, as well as the necessary coding for localization and position control.
(Source and photos: Zhengyang Lu)
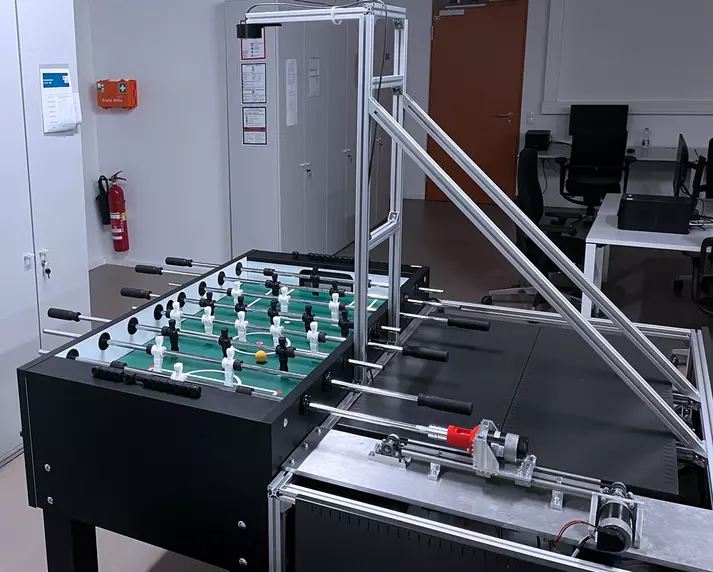
AI-controlled soccer table
This project by the Technical University of Darmstadt blurs the lines between man and machine. The AI-controlled soccer table was developed as part of a research project focusing on robust algorithms for AI-powered robotic systems. The soccer figures are driven by Nanotec’s DB59 brushless DC motors and the C5-E high-performance controllers, enabling matches against AI.
(Source and photos: Janosch Moos)
Six-axis robot with articulated arm
As part of his "Mechatronics Robotics” master’s program, a student at the TU Munich developed a six-axis robot. Its articulated arm is particularly suited for dynamic positioning tasks.
The belt-driven lightweight robot is equipped with two DFA68 and four DF45 external rotor motors, controlled by a CL4-E controller and addressed via the CANopen interface.
Nanotec funded the drive components.
(Source and photos: Adrian Prinz)
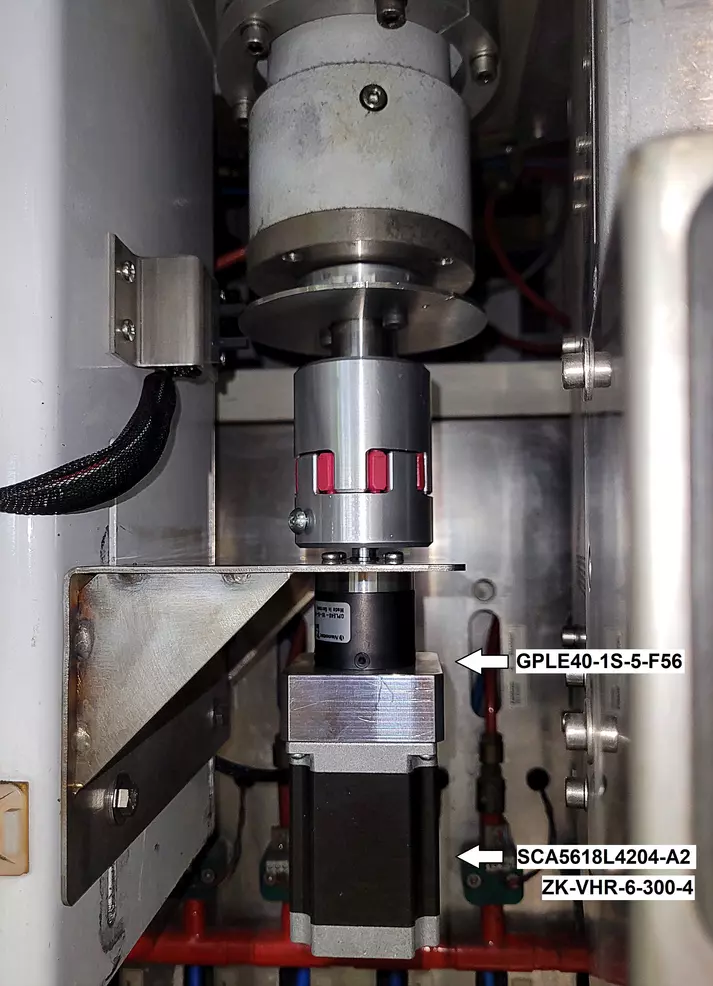
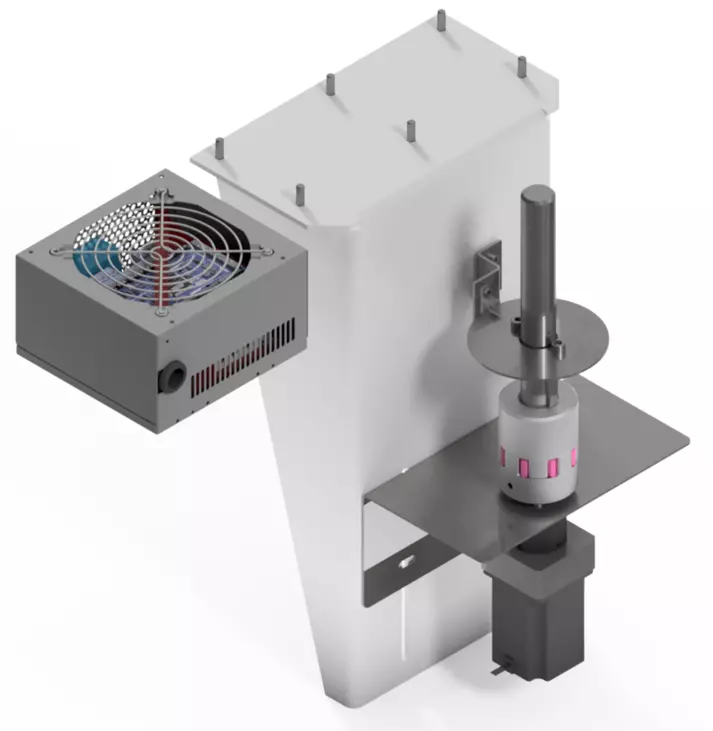
PVD system with optimized table drive
As part of a Master's project, students at Niederrhein University of Applied Sciences upgraded the table drive of a PVD (Physical Vapour Deposition) system. Their challenge: The rotary table of the PVD coating system should be designed so that samples can be taken at a defined position and the rotation speed is finely adjustable.
The future mechatronic engineers developed the software and control system themselves. Nanotec provided the mechanical components. With the support of the SCA5618 stepper motor and the GPLE40 planetary gearbox, the system was successfully put into operation.
(Source und photos: Nikolai Desch)
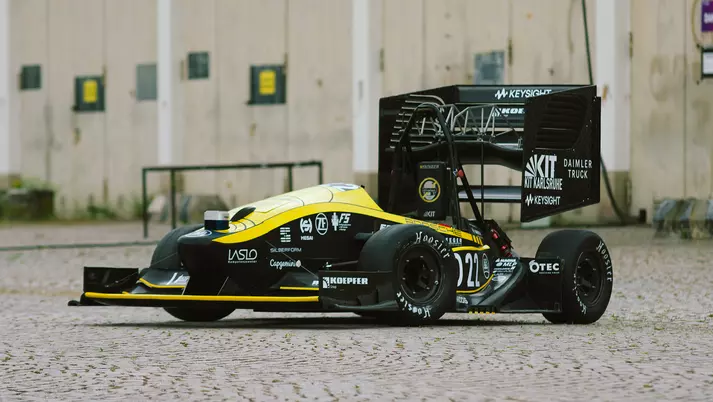
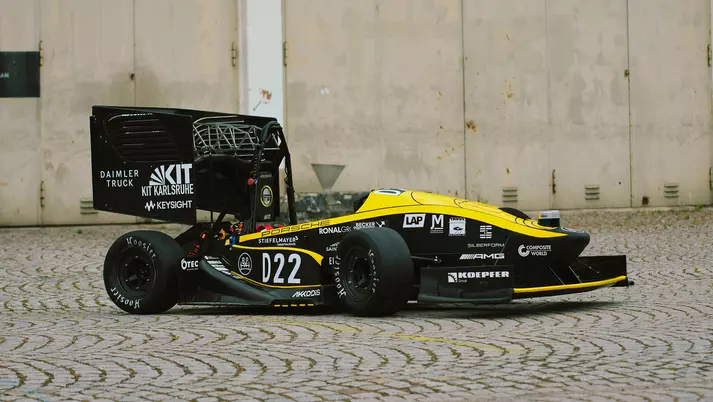
KA-RaceIng on the path to success
Under the name "KA-RaceIng," the Karlsruhe Institute of Technology is at the forefront of the Formula Student competition. With their newly developed autonomous single-seater KIT23, the students aim to continue their streak of success.
Playing a central role: the brushless DC flat motor DFA90 and the high-performance controller/drive C5-E-2. Sponsored by Nanotec, these products, along with a transmission system developed by KA-RaceIng, ensure precise and swift steering that meets the demanding requirements of the Formula Student competition. The team has high expectations for the KIT23, aiming not only to secure a place on the winner's podium this time but also in the upcoming seasons!
(Source and photos: Simon Enderle)

Easy battery transport with Os.cart
The Os.car Racing Team from FH Campus Wien regularly faces the task of lifting and transporting their racing car battery, which weighs up to 100 kg, to the charging station. To simplify this process, they have now introduced their official transportation cart called "Os.cart" which was developed as part of a diploma thesis at HTL Rennweg.
Here's how it works: Using a screw-driven and height-adjustable scissors mechanism, Os.cart moves upward until it is on the same level as the cockpit of the race car. This way the battery can be removed and installed conveniently while Os.cart provides ergonomic support with minimal effort.
Os.cart contains several components from Nanotec, including the ST6018 stepper motor, a WEDL encoder, GP56 planetary gear and C5-E controller.
(Source and photos: Kerstin Preisl)
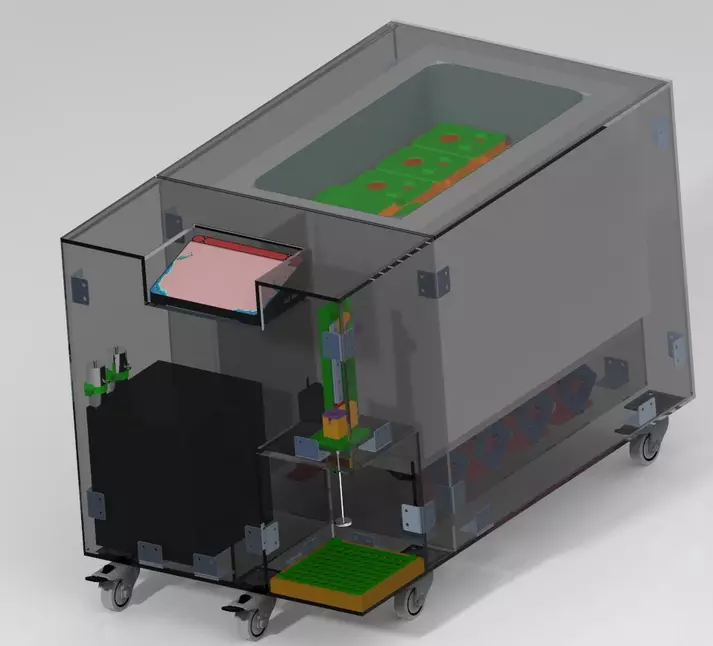
Octa-Mix – the perfect blend
The newly developed "Octa-Mix", constructed by students at HTL Rennweg, creates the perfect beverage mixture. This device combines different liquids, according to specific instructions, and quickly serves the desired mix.
Users can define the mixing ratio via the touch display or Android app. The Octa-Mix contains eight beverage tanks and can handle complex recipes, including a variety of liquids, such as water, syrup, or concentrate. The precise dosing is ensured by a system of peristaltic pumps, which are controlled by nine ST4118 stepper motors, provided by Nanotec, as part of the project funding for universities.
(Source and photos: Fabian Gutruf)
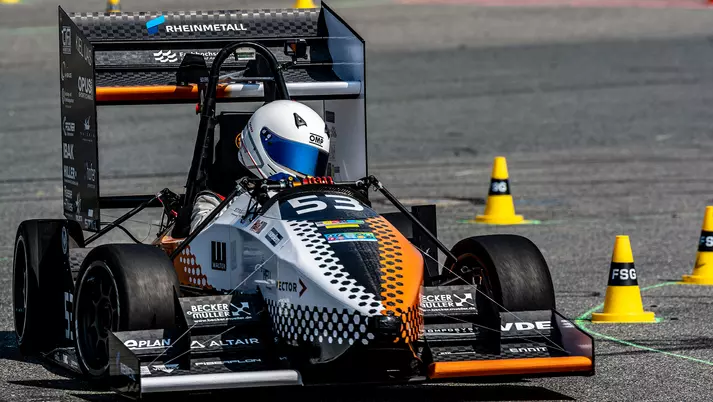
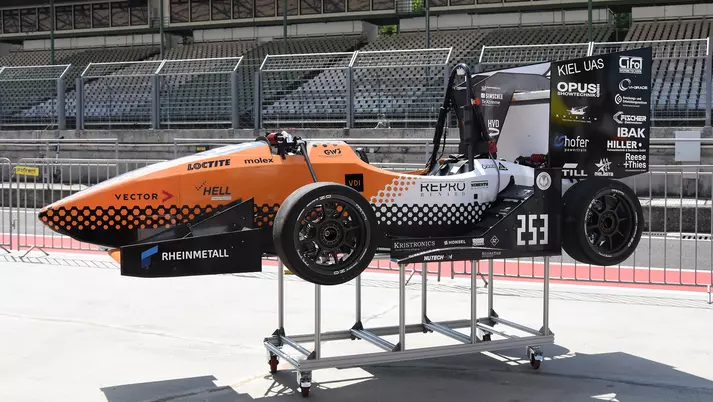
Raceyard goes Driverless
With Team "Raceyard", Kiel University of Applied Sciences’ students are an integral part of Formula Student, the international design competition for racing cars. The goal was to further develop the T-Kiel A 22 E single-seater into a driverless vehicle.
The teams’ greatest challenge was converting the manual steering system to autonomous driving mode. By providing the high-performance brushless DC motor DB43, combined with the GPLE40 planetary gearbox, NTO3 encoder and C5-E controller, Nanotec supported team Raceyard with the components needed.
(Source and photos: Bo Kluth)
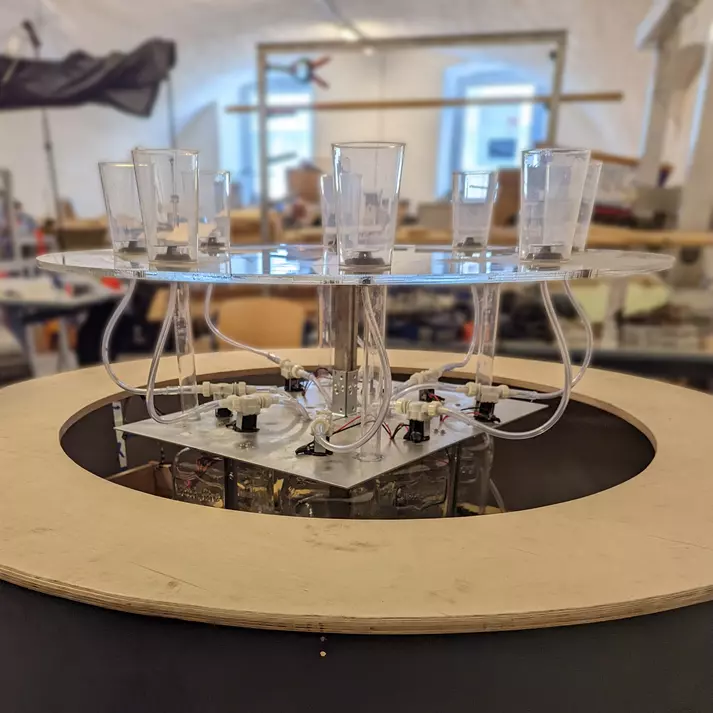
RoundT – the transparent drink tap system
The RoundT was developed by four students from HTL Rennweg. As the name RoundT suggests, the device in question is a round table.
Located in its interior is a refrigeration chamber with six beverage containers, each with a capacity of four liters. The chamber manages to cool down the beverages to 14 °C within 20 minutes.
The inner part moves a motor + gear wheel + lead screw connection up and down by means of an app. For this purpose, Nanotec supplied the ST5918L2008-B stepper motor. It drives a gear wheel, which moves the lead screw as well as the connected inner part. To tap a beverage, one simply places a cup on one of the eight tapping valves (self-produced) and selects the desired beverage via an app. Thanks to the transparent tabletop, the user can see how the tubing system fills the cup from below.
(Source and photos: Dominik Michalski / Niklas Eichelberger)
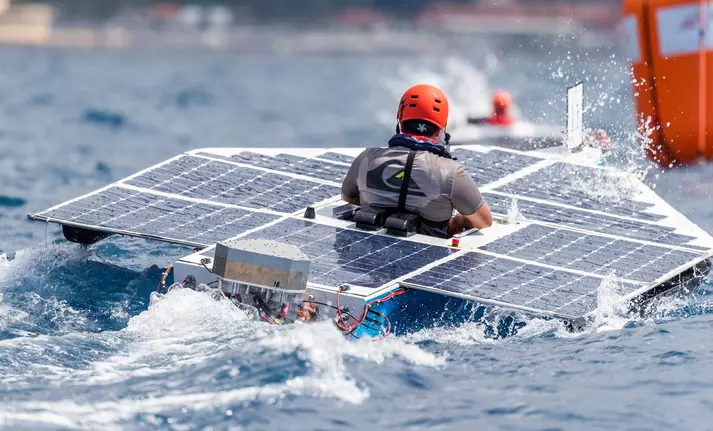
Solar Boat
Técnico Solar Boat is a university project, made up of a group of students from the engineering courses of Instituto Superior Técnico.
This season, they are building their second boat, the SR02. The SR02 will be 6m in length and 2m wide, and it will be lighter, faster and more efficient. To accomplish the set goals, the team is working on a hydrofoil system that lifts the boat out of the water to reduce drag. For this the students have an electronic control of the angle of attack of the underwater wings. This control is done with sensors and actuators, and these actuators come from Nanotec.
The project group uses three stepper motors all controlled by N5-1-2 controllers, fitted with NOE2 encoders to know the exact position of the hydrofoils. These products have helped the team with detailed datasheets and the Plug and Drive Studio software in which they can try all the different modes of operation and easily set all the desired parameters.
(Source and photos: Sebastião Beirão)
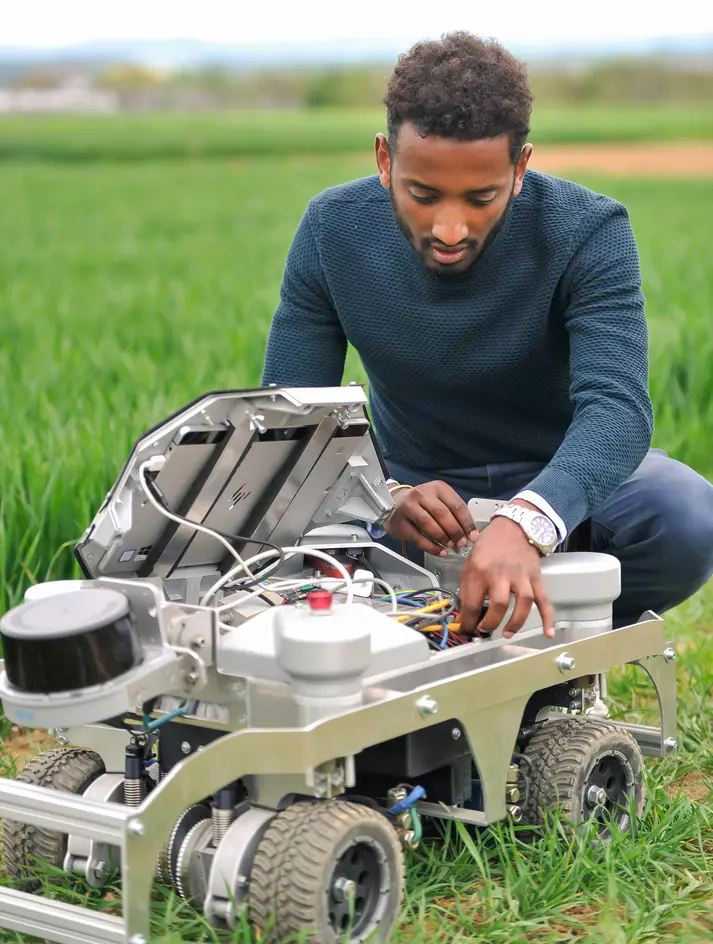
Autonomous field robot
At the University of Hohenheim research is currently being conducted on the future use of autonomous field robots in agriculture. For this purpose, a team of students regularly participates in the "Field Robot Event". The goal of this annual robot competition is to have small robots autonomously perform various tasks in agriculture that were previously considered too time consuming and unprofitable.
Thanks to the support from Nanotec, it was possible to program and construct a new robot named "Goliath". The machine is designed so that it can navigate between the rows of plants and be used for autonomous monitoring or small manipulation tasks in the field.
Goliath has a single-wheel steering system and a single-wheel drive in which the motors PD4-C5918M4204 and PD6-N8918S6404 are used. The motors are controlled via ROS (Robot Operating System) and CANopen. Laser scanners and cameras help the robot detect his environment.
(Source and photos: Jonas Esterl / Dr. sc. agr. Dipl.-Ing. David Reiser)
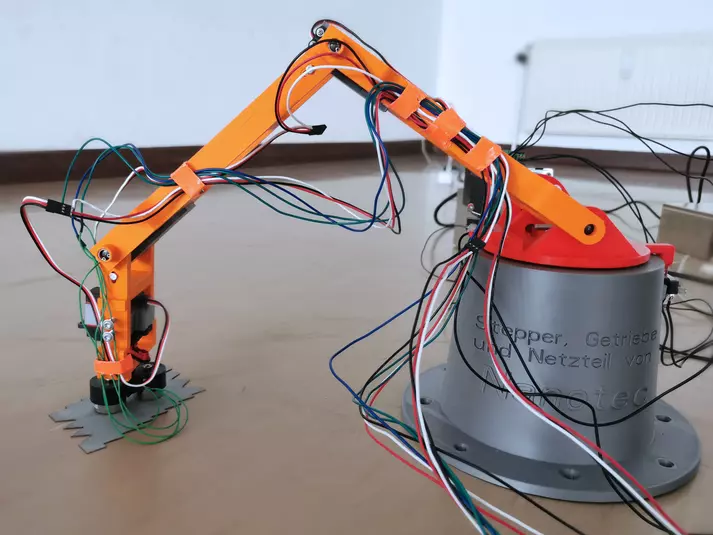
Pick’n’place robot
A team of students from HTL Rennweg constructed a pick'n'place robot with five rotating axes. The robot can pick up an object and set it down at another location.
To make the robot move, the team used two PD4-C6018L4204-E-01 motors with integrated controller and the GP56-S1-3-SR high-torque planetary gearbox from Nanotec on the two main axes.
The robot is quite flexible and is also equipped with electromagnets for gripping parts that cannot be lifted magnetically. On the other three axes, the group installed low-weight modelling servos.
(Source and photo: Silas Amesmann)
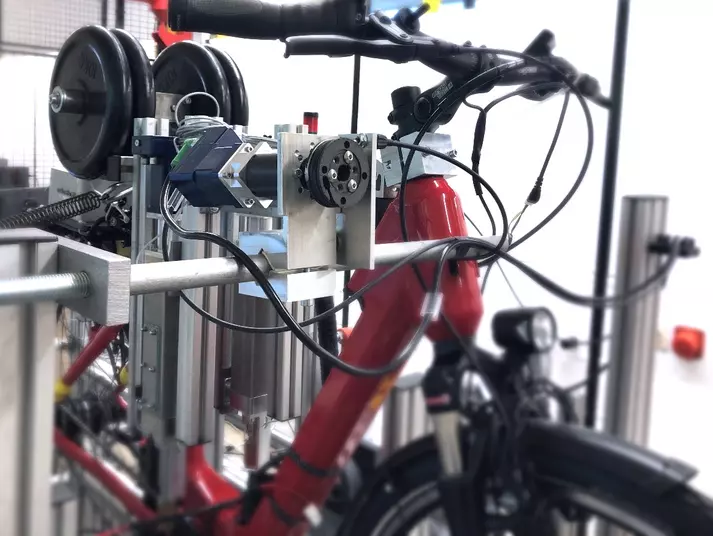
E-bike test bench
Electric bikes are no longer a niche product used by just a certain demographic. Consequently, the demand for high-quality e-bikes has been growing for some time. To obtain a consistently high quality in the production of the e-bikes, Aalen University has developed a test bench that can be used to test the bicycle as a complete system with respect to its quality. Up until now, these tests have predominantly been component tests that represent reality only to a limited degree.
The unique feature of this test bench is that the human pedalling behavior is reproduced 1:1. The simulation is enabled by an intelligent, sinusoidal control of the driving torques of the motors, which simulate the rocking motion of a pedaling cyclist.
The gear-shifting behavior of the bicycle rider is reproduced by the Nanotec stepper motor PD2-N4118L1804-IP-2 (NEMA 17). The gear shift cable is coupled to this motor via a reel that winds the cable.
The team from the Faculty of Mechanical Engineering and Materials Science combined this stepper motor with integrated controller using Nanotec's own NanoPro software and controlled it via a PC.
(Source and photos: Özben Sarikurt)
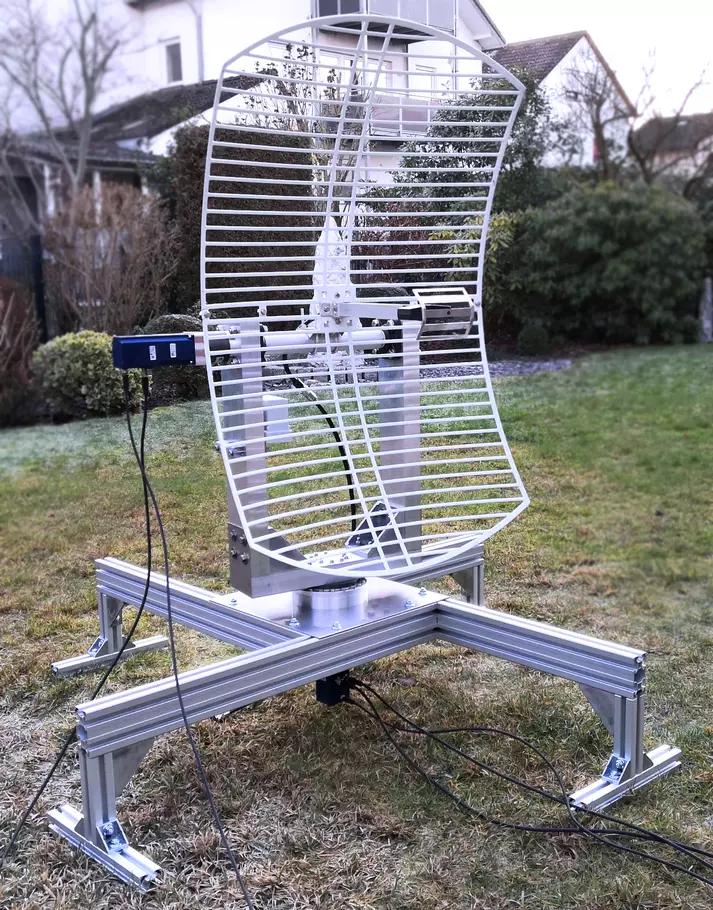
Ground station for satellite tracking
The Space Technology e.V. Group of the Technical University of Darmstadt is an accredited university group that promotes space research by students. Since its founding, the 35 students have been developing a small satellite, a so-called CubeSat.
The objective of the satellite mission is to demonstrate innovative technologies that contribute to the reduction of the hazards of space debris. To communicate with the CubeSat satellite, the team constructed a ground station that enables radio contact through the precise alignment of an antenna. Tracking of the antenna is ensured by two axes, driven by the IP65-rated stepper motor AS5918L4204-EB from Nanotec. To reach the required torques, the group uses the precision planetary gearbox GPLE60-2S-32.
(Source and photo: Fabian Burger)
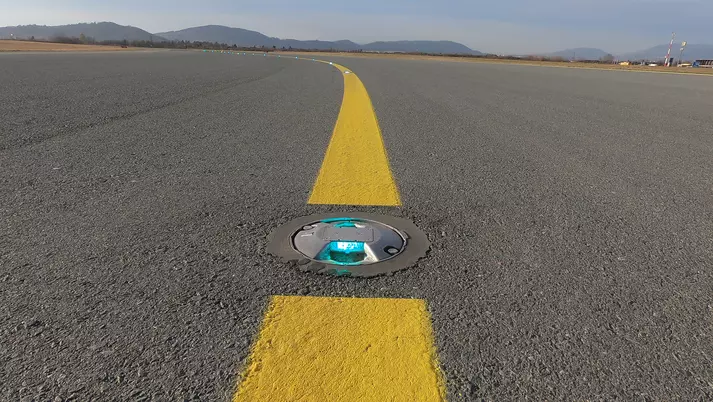
Automatic light measuring at airports
The "relight" project is a device for measuring lights that was developed by four students at HTL Rennweg in Vienna, Austria. The lights are installed in the taxiway of an airport and need to undergo regular service to satisfy requirements and to ensure the required safety. Therefore, the device measures their brightness from various positions. Because some lights are not seated in the middle of the socket, the offset must be compensated mechanically. The LA421S14-A-UKBN non-captive linear actuator from Nanotec fulfills this requirement precisely and automatically.
The measuring device is used at small airports in Austria as it is a good alternative to the models available on the market.
(Source and photos: Matthias Gerber)
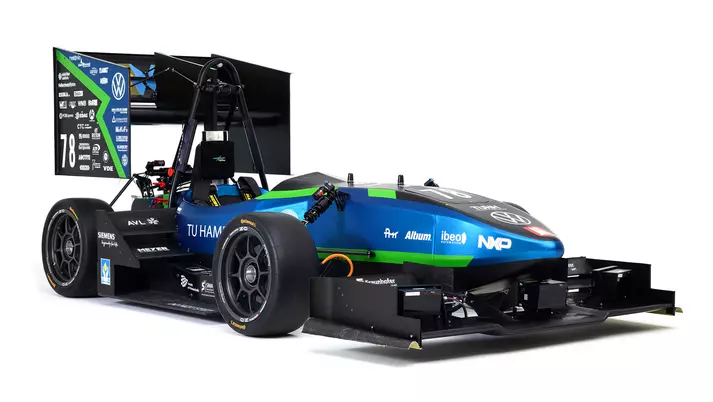
Autonomous steering for race cars
The e-gnition Hamburg team at the Technical University of Hamburg (TUHH) has been building electrically powered race cars since 2011. The group consists of around 60 students and successfully takes part on a regular basis in the Formula Student, the world's biggest engineering competition. In the 2020 season, the team for the first time entered the same car with combined design concept in both the driverless and electric competitions.
Various motors and controllers are used in the autonomous steering system of the race car and, thanks to Nanotec, keep the car on track. In the 2021 season, the students used the CL4-E-2-12 motor controller to drive the steering wheel-mounted electric motor, which is turning the steering in the same way as a driver does.
Further technical information as well as photos can be found at https://en.egnition.hamburg/
(Source and photos: Ole Ramming)
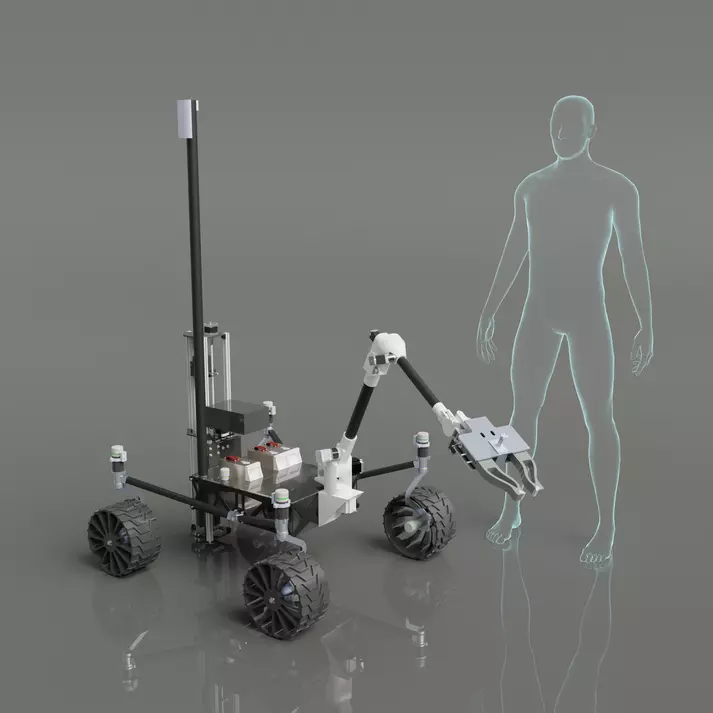
Mars Rover
STAR Dresden e.V. is a student work group for space travel at TU Dresden (Technical University of Dresden). It is made up of approximately 30 members from various degree programs, including engineering, physics and medicine. The group developed a Mars rover and used it to participate in the European Rover Challenge (ERC) in Poland where student teams from around the world competed against one another with their self-constructed rovers.
The Mars rover built by Star Dresden e.V. is named ELECTRA (Expeditionary Lightweight Extraction Collection Transportation Rover Assistant). The vehicle was intended to simulate use on Mars and to support astronauts on the simulated Mars surface. The team was located in a separate tent and controlled the rover remotely. Tasks to be performed by the rover included, among other things, taking soil samples, taking pictures, operating switches on a control panel and connecting a high-current plug – all as autonomously as possible and in a very confined space. Moreover, the rover had to use QR codes for orientation and had to follow a specified route over difficult terrain.
The rover has four wheels for mobility. The wheels can be turned nearly 360° along their vertical axis. For steering the rover, the team installed the DF45L024048-C2 brushless DC motor, combined with a GPLK42-56 lightweight planetary gearbox. For the drive a DF45L024048-A2 brushless DC motor with an GP42-S2-46-SR high-torque planetary gearbox was used.
(Source and illustration: Elias Ortlieb)
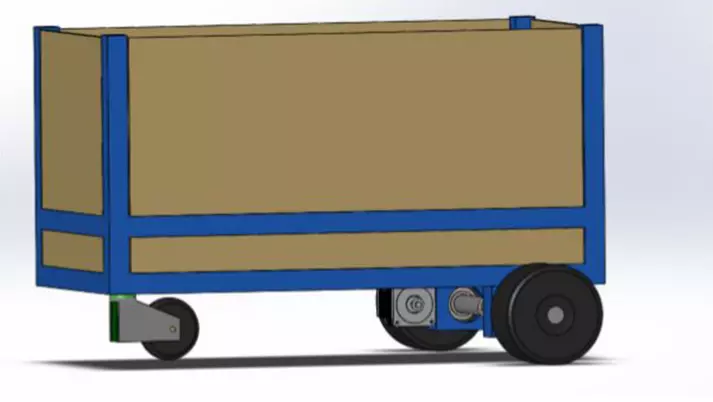
E-Trailer
The "E-Trailer" project group of the Rudolf-Diesel technical school for engineers in Nuremberg, Germany, has planned, designed, and built a self-driving trailer. To enable the E-trailer to drive autonomously, it was fitted with its own electrical drive on the rear axle. The front wheel, which is also driven by a motor, is used to steer. The trailer is capable of steering, braking, and keeping distance autonomously.
To steer the front axle, the four-member project team needed a stepper motor with DC voltage (24 – 48 V). The team opted for the PD4-C5918M4204-E-01 brushless DC motor with integrated controller and the GP56-S1-7-SR high-torque planetary gearbox from Nanotec.
(Source and illustration: Sebastian Blank, Maximilian Lenk, Andreas Ortner, and Philipp Geitner)
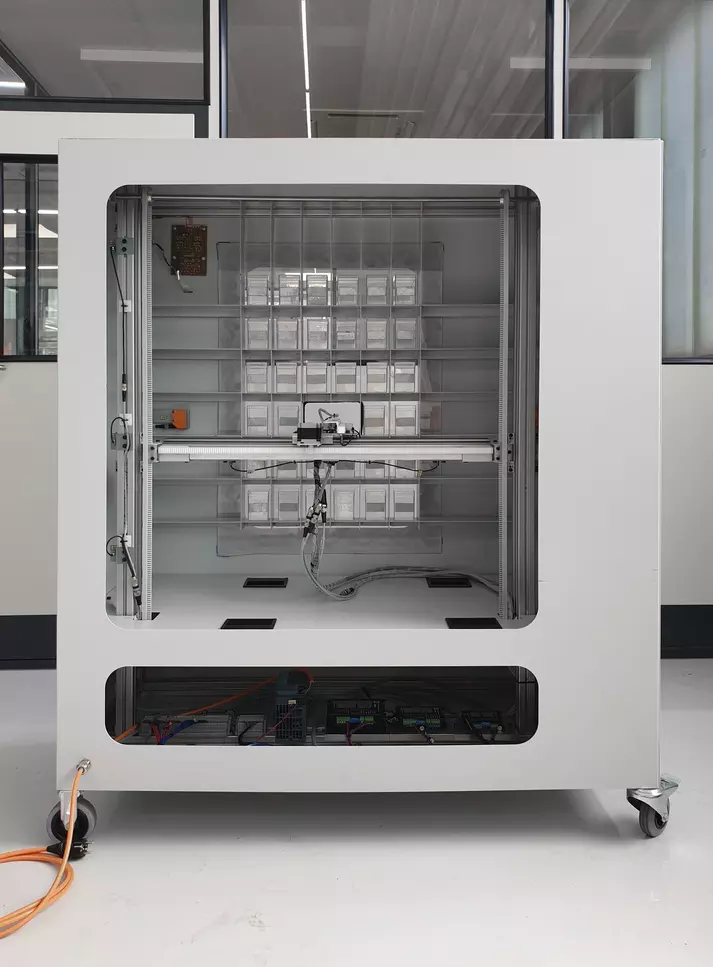
Automated spice rack
Within the scope of the SIA project (Student Engineering Academy), students at the Rosenstein high school planned, designed and implemented an automated spice rack. Controlled by means of a microcontroller (Arduino), it automatically moves to shelf compartments and dispenses the container located there via a hatch.
Thanks to the use of stepper motors from Nanotec (1x ST8918L4508-B, ST5918S1008-A and ST4118L1206-A), the students were able to optimally realize the movement concept of the automatic spice rack.
Source and photos: Jens Gruber
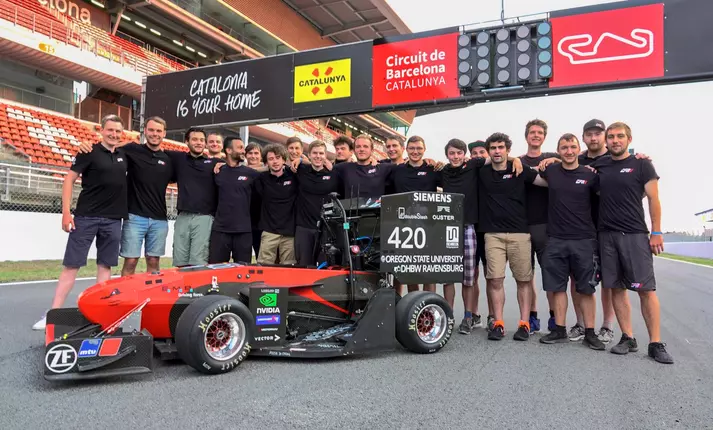
Autonomous steering system
The Global Formula Racing Team is an international racing team from the Baden-Württemberg Cooperative State University (DHBW), Ravensburg, and Oregon State University, USA. The students work together to build two race cars and take part in international competitions against other teams from more than 500 universities.
At Formula Student Germany on the Hockenheimring and Formula Student Spain on the Circuit de Barcelona-Catalunya, the team from DHBW Ravensburg achieved good results in spite of the still relatively new design.
One of the many challenges that had to be overcome by the team while building the vehicle was the construction and design of a steering system. The system needed to meet the requirements for use on the race course. With two PD6-CB87S048030-E-098, Nanotec Electronic provided motors for the steering of the race car. Thanks to this DC motor, it was possible to build a functional car with the steering behavior of a human driver in autonomous mode.
Source and photos: Marko Bausch
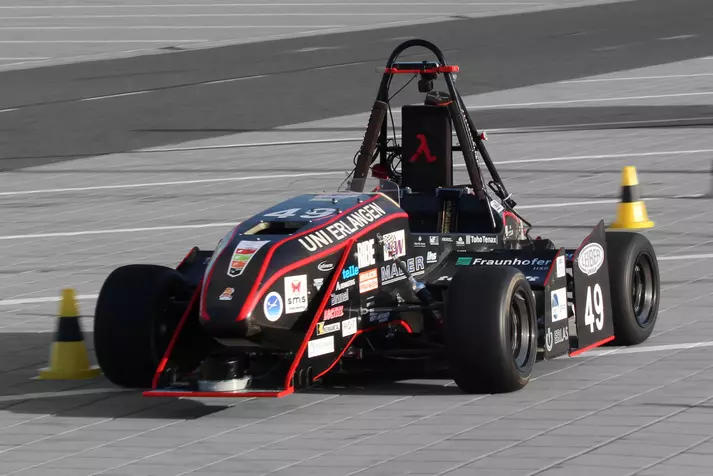
Automated Steering
The Driverless team of High-Octane Motorsports e.V. from the University of Erlangen-Nuremberg converted a standard go-cart into an autonomous driving vehicle in one year. Among other things, additional sensors, a computing unit and electrical actuators were added for controlling the vehicle. The passive brake system is actuated via the control by means of stepper motors. The team used the ST4118D1804-B stepper motor from Nanotec for this purpose. For other important components – such as the steering – each of which is subject to high requirements in the areas of agility, force and reliability, the team used the ST6018L3008-A stepper motor with the GPLE60-1S-8 gearbox. High-performance and space-optimized designs could thereby be implemented.
Source and photos: Richard Stierstorfer
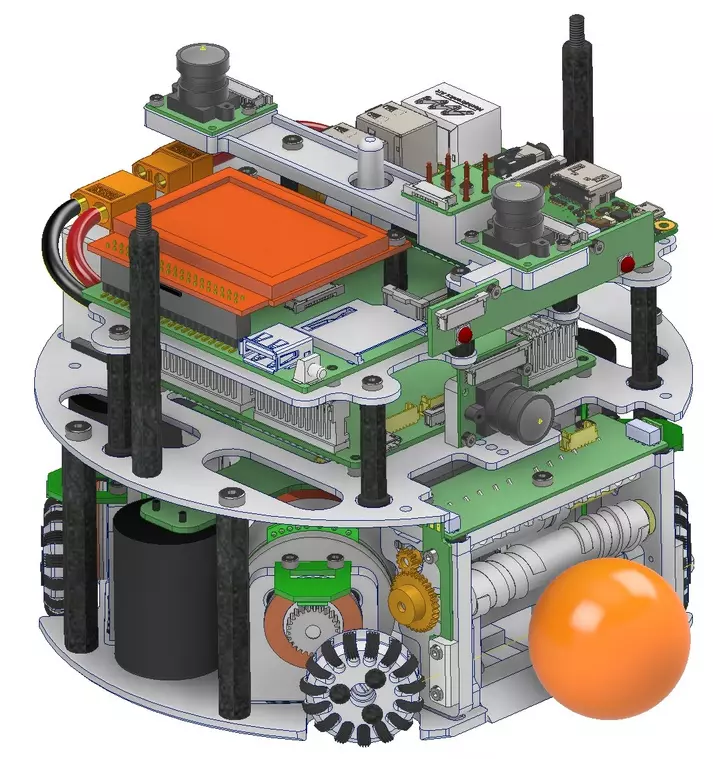
Soccer-playing robots
At the Baden-Württemberg Cooperative State University (DHBW) in Mannheim, the TIGERs develop small, soccer-playing robots that participate in the annual world championships of the RoboCup Federation.
The robots are self-constructed from scratch and play entirely without human intervention. At the last world championships, the Mannheim TIGERs were honored with the "Excellence Award" for outstanding scientific contribution and overall performance.
In the fourth generation of robots, the motor was replaced with a more powerful variant: with 65 watts, the DF45L024048-A2 is ideal for this purpose, since the installation space is so limited that the smaller connection board of the A2 variant makes a big difference.
Source and photos: Andre Ryll
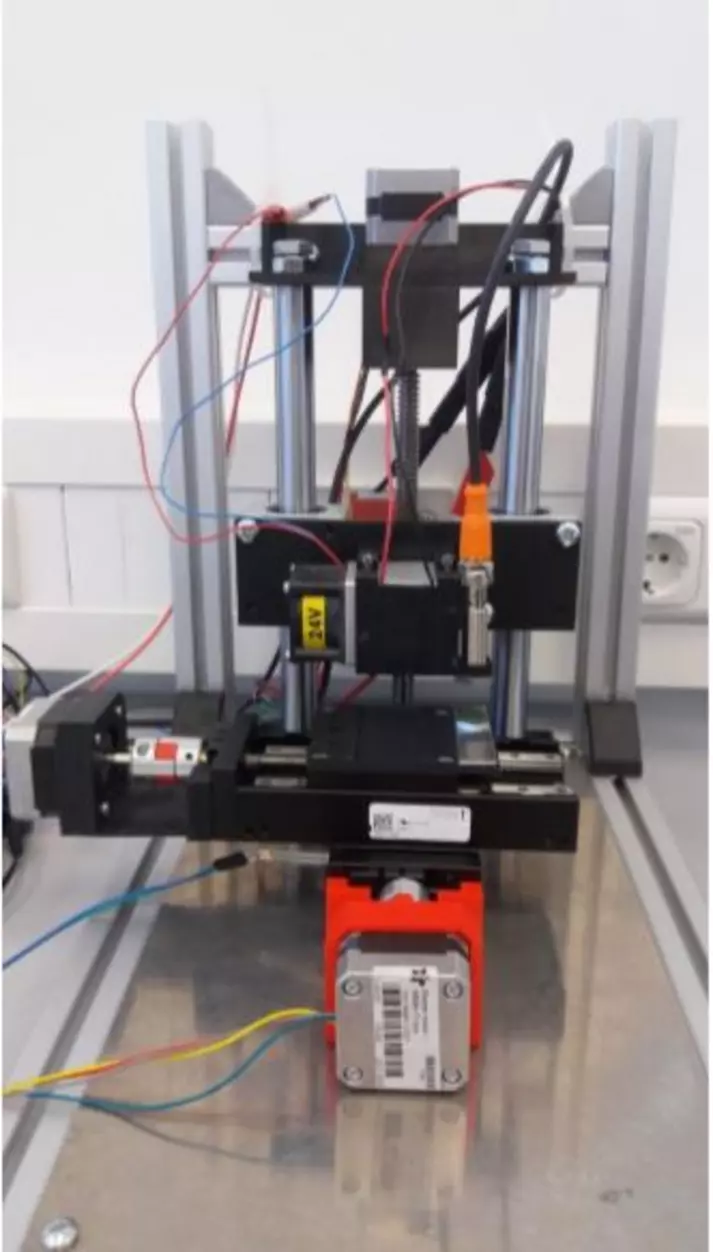
3-axis precision positioning system
At the South Westphalia University of Applied Sciences (FH Südwestfalen) in Iserlohn, a student developed a microdispenser with a 3-axis precision positioning system. This microdispenser uses an innovative method for dosing liquids that can dispense a very small quantity.
Since the liquid is not dosed through a hollow needle, the dispenser is not dependent on the liquid's viscosity. This also eliminates frequently occurring cleaning processes. The C5-01 open-loop stepper motor controller from Nanotec was used in the microdispenser.
Source and photos: Aingharann Pathmanathan
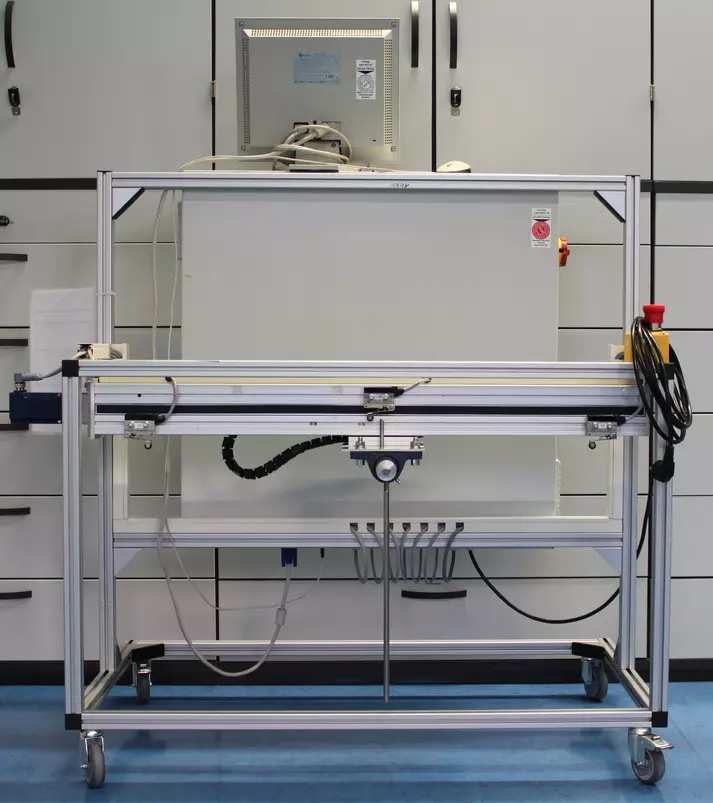
Inverted pendulum with programmable logic controller
At the Nuremberg Institute of Technology (Technische Hochschule Nürnberg), students have constructed an inverted pendulum with a programmable logic controller. The rigid pendulum rod can rotate freely at its attachment point. Through a controlled back and forth movement of the bearing point, the rod can be held in an upright state and interfering influences compensated for. Thus, the control task is the stabilization of the pendulum rod in its upright, unstable equilibrium position.
A linear axis is used to move the attachment point of the pendulum rod. The AS5918L4204-ENM24 stepper motor and the N5-1-1 motor controller from Nanotec are used as the drive system.
The use of the closed-loop technology offers numerous advantages:
- Smoother motor operation
- Faster acceleration
- More precise positioning
- Less warming of the motor
Source and photos: Simon Northoff
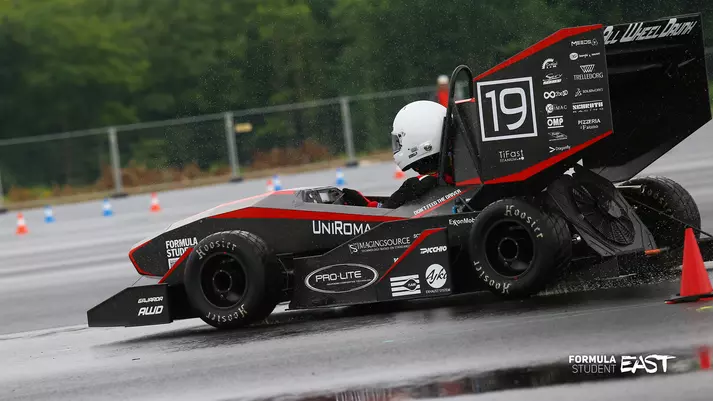
Autonomous Car
“Formula Student” is a worldwide design competition in which a group of university students, coming from every part of the world, present a formula-style race car prototype. This year, the Formula Student team “Sapienza Corse” (“La Sapienza” – University of Rome) tried to implement an ETC system in his car “Gajarda AWD”. An electronic throttle control allows an easier driveability, as the driver is not a professional one. Moreover it may provide significant improvement in terms of car efficiency.
The stepper motor ST2818L1404-A has been the key element of the entire system: it can provide with safety and precision the movement of the throttle valve, not affecting the rapidity of reaction nor the weight of the car. The motor also give us the necessary torque not to use a large gearing system.
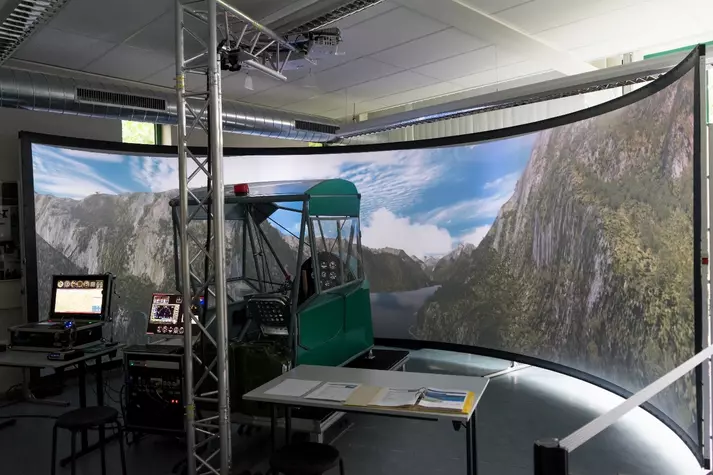
Force Feedback Joystick
Students of the University of Kassel came up with the idea of building a Fieseler Storch flight simulator. In its current version, the simulator features a 180° screen that allows the pilot to get a realistic simulation of a propeller-driven aircraft from 1936.
A haptic joystick will be integrated next, which will simulate the wind forces acting upon the rudder and flaps. To implement the feedback circuit, two stepper motors (PD4-C6018L4204) from Nanotec were used. The forces are transmitted via toothed belts at a ratio of 1:5.
Source and photos: Daniel Strawe
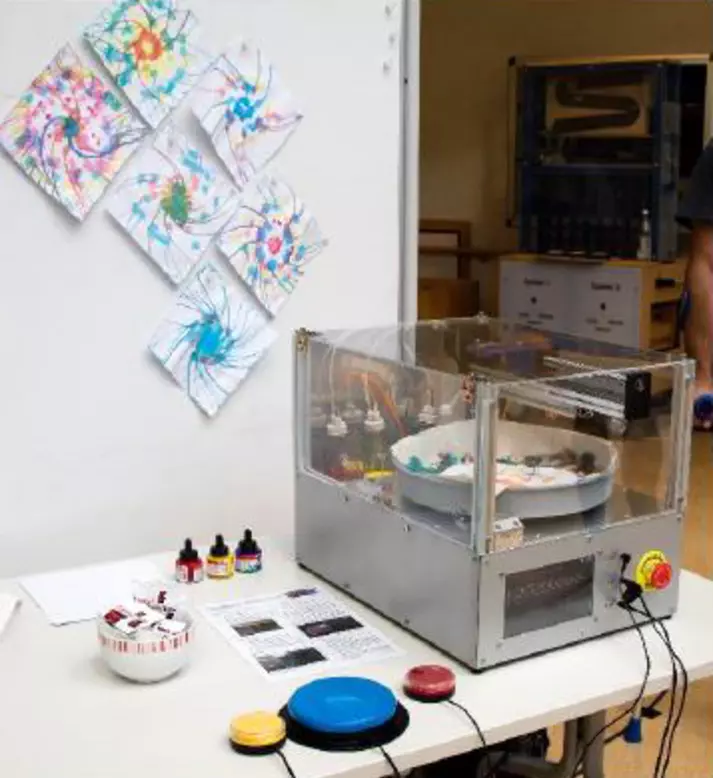
A team of six students from the University of Augsburg designed and built a machine that can paint color patterns for the "Fritz-Felsenstein-Haus." The facility is home to people with various disabilities.
The Paint Catapult project uses the ST8918M6708-B high-torque stepper motor from Nanotec to drive a rotary plate. The students installed a sheet of paper on this plate, onto which paint is dripped using a linear carriage and pump elements. The rotational force guides the drops of paint outward, which results in unique patterns, depending on the speed and application position. The speed is set on the touchscreen display after starting up. The three buttons on the screen serve to select the color, spindle position, and apply the paint, making the device easy to operate.
Source and photos: Patrick Lebmeier
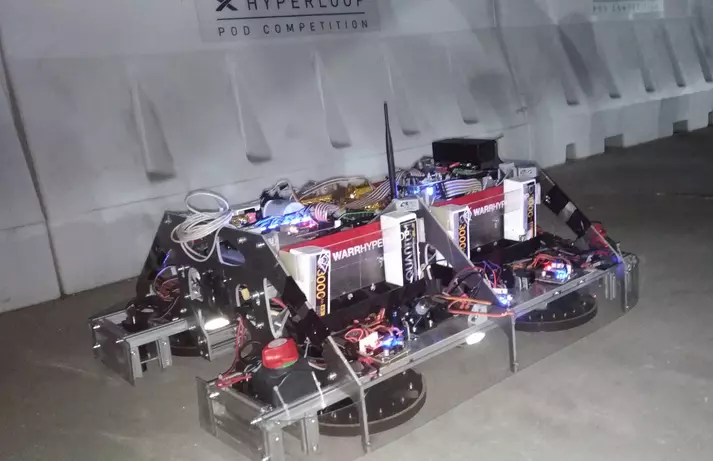
The WARR Hyperloop team at the Technical University of Munich built a floating pod. Four linear actuators lift the pod, so that it can start the hovering drives. This is done using four L3518S1204-T6X1-A25 linear actuators size NEMA 14 from Nanotec.
Once the drives are rotating, the "Nanotec legs" are automatically retracted and the pod floats magnetically. Payloads weighing up to 50 kg can be transported.
Source and photos: Domenik Radeck
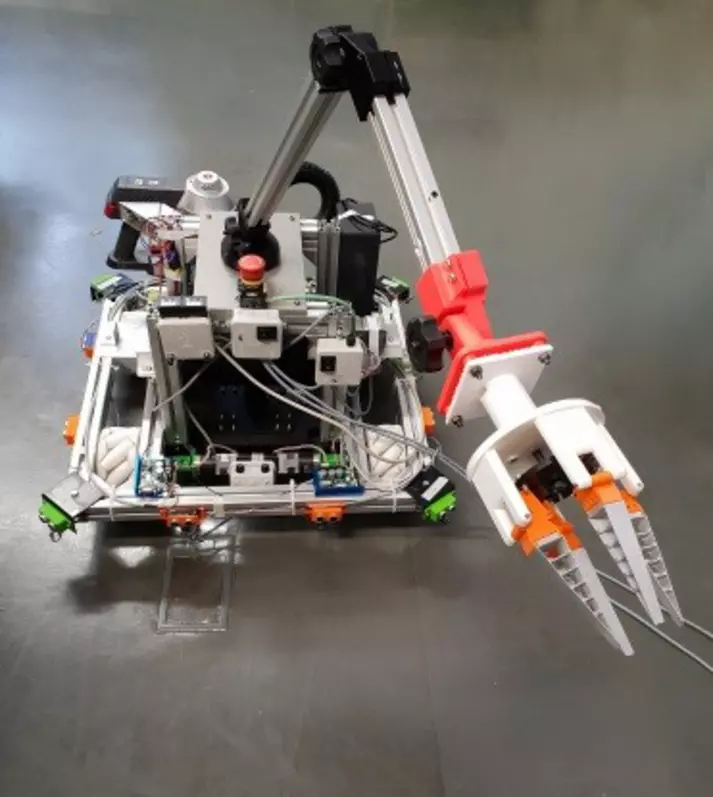
During the summer semester 2017, students at Munich University built a household robot that can autonomously move around and vacuum. The robot features a gripper arm to pick up and transport objects.
The students installed a high-torque stepper motor ST5918L2008-B size NEMA 23 and worm gear GSGE60-25-1 from Nanotec in the robot's arm.
Source and photos: Philipp Heckenmüller
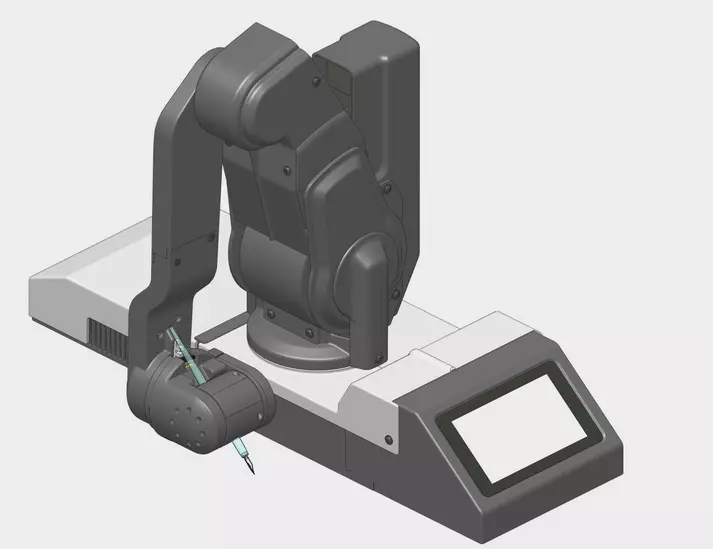
The student project "Manuscript Writer" is about a robot that is capable of mimicking handwriting. The robot's stylus was equipped with BLDC motors from Nanotec. The powerful BLDC motors size DB59 were used as internal rotor motors.
For the robot to be able to retract from any given position, the two large motors (axes 1 and 2) require a minimum torque of 21 Ncm, and the small motor (axis 3) 4.5 Ncm: this happens as soon as the robot's arm is fully extended at a 90° angle.
Source and photos: Mathias Mettauer

The "Easy Going" touring ski binding is a project by students from HTBLA Rennweg in Vienna. This ski binding features automatic stepped adjusting depending on the uphill or downhill gradient. The binding adjusts correspondingly in automatic mode. If the ski tourer selects manual mode, the level can be selected at the push of a button.
Each binding features a motor, battery, microchip, and a wireless module. Two linear actuators LSA201S06-A-TDBA-102 from Nanotec size NEMA 8 (20 mm) are used. These facilitate the inclusion of space-saving linear axes.
Source and photos: Christopher Muhr
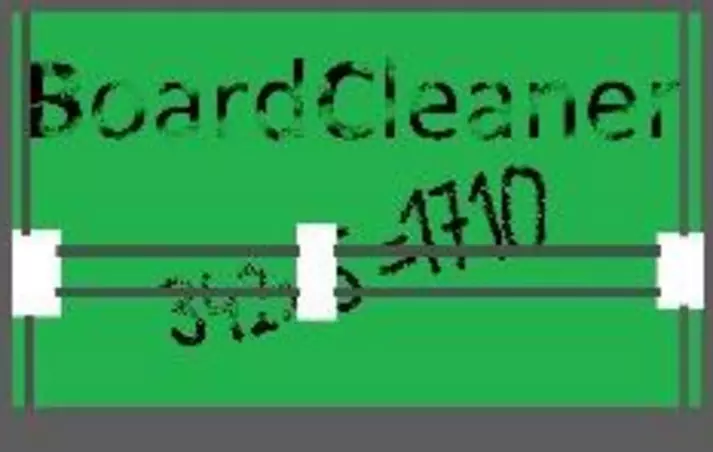
The team at HTL Rennweg in Vienna developed a 2-axis robot in their robotics class, which is capable of cleaning and wiping blackboards (60 cm x 45 cm).
The students used the high-torque stepper motor ST5918M3008-A size NEMA 23 and two stepper motors ST4209L1704-A size NEMA 17 with the economy planetary gearbox GPLE40 for the project. The ST4209L1704-A handles the movements in the X direction, while the second and third stepper motors are responsible for the Z direction.
Source and photos: Lukas Satzinger
The declared goal of the "Formula Students" is to design and build a race car within a year and drive it over the finish lines of Europe's racetracks. The e-gnition team of the TUHH (Technical University of Hamburg-Harburg) has successfully participated in this contest with its electrical race car every year since 2012. The team consists of almost 60 students from all TUHH degree programs. In 2017, they ranked 9th amongst participants with electric vehicles at the "Formula Student Germany" which takes place annually at the Hockenheimring race track.
New in 2017 was the driverless category, in which an existing vehicle is converted to a fully autonomous vehicle. In order to do this, the students used Nanotec's DB59S024035 brushless DC motor to rotate the steering shaft and thus steer the car autonomously. It replaces the hands of the driver who would normally turn the steering wheel.
The e-ignition team was delighted after the race, as their autonomously driving race car came in third in the world ranking of the "Autonomous Design Award".
Source and photos: Ole Ramming
For 13 months, a team of 21 students from the University of Leuven in Belgium worked on the Punch 2, a new solar car with which they started in the Bridgestone World Solar Challenge in Australia on October 8. The race lead straight through the Australian Outback, from Darwin to Adelaide, over a distance of 3,000 km.
This year a lot of novelties have been put in the solar car. Among other features, the Punch 2 is equipped with a unique mechanical four-wheel steering system which consists of a mechanically decoupled front and rear wheel steering. This means that the front wheels rotate with the first 90° displacement of the steering wheel. When the driver continues to turn the steering wheel, the rear wheel steering is activated additionally. The steering motion is transferred to the four wheels using steel cables.
In order to test the new system, the team decided to build a copy of the steering system. A brushless DC motor from Nanotec was used in combination with a gearbox and linked to the steering wheel to simulate the steering movements during the race. The steering forces were simulated by using strong springs which required a gearbox to provide the required torque.
Text and photos: Martijn Schaeken
Students majoring in Mechatronics and Precision Engineering at the University of Applied Sciences Munich developed an automated winding machine for guitar pickups as part of the "mechatronic integration" seminar in the summer semester 2016.
A special spring system was developed so that the enameled copper wire did not snap when it was wound onto the spool. For driving the pickup, the stepper motor ST5918 was used. With the help of a SMCI35 controller, it was possible to actuate the motor in such a way that there is a ramped increase in speed up to a threshold value when the number of windings increases. Then it rotates at a constant speed until the process is stopped.
Furthermore, by using the external linear actuator LS20, the wire is fed parallel to the rotational axis of the pickup across the whole width of the spool continuously.
From May 14 to May 15, 2016, the third edition of the Ecorace-Challenge took place in Bruges, Belgium. Seven teams competed with their scale models to win the award for the most innovative vessel, the best all-round cargo vessel, the best all-round no-cargo vessel and the the best business plan.
The awards for the most innovative vessel and the best all-around cargo boat went to the University KU Leuven for "Galena", a model of a cargo vessel designed to carry one ton of goods and sail inland waterways. In the future Galena is supposed to sail completely autonomous. The steering of the vessel is powered by Nanotec's PD4-N5918L4204 connected to Nanotec's gearbox GPLE60-2S-16.
We congratulate Dominic Libanio, Christian Schorr and Pascal Lindemann on winning first place in the regional "Jugend Forscht" competition and on coming in second in the Ideenwettbewerb Rheinland-Pfalz ("Ideas Competition"). The project, which Nanotec supported with motors, dealt with the development of a hand therapy device.
Often, the results achieved by hand surgery and follow-up therapy are not satisfactory because physical therapy is neither prescribed nor performed to the extent necessary for reasons of cost and time. The consequences range from elementary restrictions in movement to significant disruptions in the fine motor skills. The therapy device for the hands shown here is intended to support physicians and physiotherapists. Each finger receives an individually fitted mechanism that is driven by a Nanotec linear motor.
At a Berlin school, the students of Applied Industrial Electronics were asked to develop a robot that builds a wall of any height and shape on the basis of custom software. Controlled by an on-board ATmega32, a virtually autonomous wireless vehicle was then constructed within six months. This vehicle is powered by two on-board Nanotec stepper motors, each driving a shaft-mounted, exterior aluminum wheel, thus providing precise position control. Stability is ensured by two supports on the ground at the front and back that slide when the vehicle is in motion and bear part of the vehicle's weight. A linear actuator on the front drives an arm up and down a linear guide. Equipped with an electromagnet, the arm lifts and places the wooden blocks, which are fitted with a metal plate, in a predetermined position. The vehicle's power supply is ensured by means of a 12V lithium-polymer battery. With the help of an intuitive user interface the user controls the vehicle as it travels between the base station and building site to erect a wall of variable height.
Marc Zechel, Robert Fibich
Since 2009, the institute for Mechanical Engineering at the Westphalian University of Applied Sciences in Gelsenkirchen has held an annual competition where teams of students develop a machine that has to fulfill a specific task. This year the challenge was to construct, manufacture and program an automated bottle opener for crown corks. After opening the bottle, a defined amount of the drink should be poured automatically into a glass. The winner of the 2015 competition is a bottle opener where the four-member construction team had selected the linear actuator LS4118S1404-T6x2-75 from Nanotec for opening the bottles – the decisive factors were speed and reliability.
The purpose of the Mechatronics and Precision Engineering project module at the University of Applied Sciences Munich is to create a finished product, including presentation and demonstration, from a project idea or an existing project. The students of the 2015 summer semester embarked on designing a peristaltic pump with a delivery rate of one liter per minute. This involved writing the necessary software, building the pump and taking it into service – all with a budget of under 100 euros. The team therefore used the 3D printer of the University of Applied Sciences Munich to produce most parts of the construction. The peristaltic pump was controlled using an Arduino Micro which was responsible for communication with the PC, actuation of the motor and evaluation of the sensors. The board was soldered together in the electronics lab of the university and accommodates the µC, parts of the power supply system, and the motor driver. The speed is monitored by means of a perforated disk and evaluated using software. To allow the user to operate the pump, the group wrote a front end using C-Sharp. A Nanotec stepper motor provides the central interface between the software and the design part of the peristaltic pump.
At the Institute for Applied Theater Studies at the Justus Liebig University Giessen, a student project had the task of reconstructing the Kentucky Derby – a country fair game booth. In this game of skill, players adroitly maneuver game balls to urge their mechanical horses toward the finish line. Unlike the archetype, however, this new version has no direct interaction between the players and the course of the game. Instead, the participants are seated in another room where the game supervisor observes them on a camera. The more enthusiasm the players demonstrate as they encourage their horses toward the finish line – by shouting or clapping, for example – the faster the game supervisor moves the horses forward. The horses are powered by Nanotec stepper motors of type PD4-N6018L4204. These are controlled by the same software as the light and sound installations – a perfect combination of mechanical elements and audio-visual media.
Nanotec Electronic was one of the supporters of the MALOMAT project, which was developed by students at the University of Applied Sciences Augsburg, to provide severely handicapped children a possibility to paint a canvas on their own.
The Fritz-Felsensteinhaus in Köngisbrunn is a school for physically and mentally disabled children. Painting takes an important part in their education. This is often only possible with a great deal of effort because the children are unable to paint on regular canvasses on their own. They choose a color and indicate to their tutors which part of the canvass is to be painted. The teachers use paint tubes and allow the paint to run down the canvass from the selected point.
The MALOMAT allows the pupils to do the painting on their own. After some brief preparatory work, it is possible to paint lines in three different colors. The two programs can be controlled fully by one or more children, whereby different levels of difficulty are also possible. Nanotec supported the project by providing a gear motor and a controller.
In the winter semester 2014/2015, mechatronics students at the Karlsruhe University of Applied Sciences developed a table hockey robot as part of a project study. The robot is supposed to replace a player and play against a human opponent, acting completely autonomously and making decisions about the play situation by itself. Both the puck position and its speed are registered by a sensor system and processed by evaluation electronics. The data is then sent to the mechanically-controlled pusher, so that it can move to a particular position and push the puck back. Nanotec stepper motors are used to move the carriages to which the pusher is fastened. The ST5918L4508 provides the right torque for this application and is operated here by the SMCI35 controller.
Source and photo: Jakob Bokemeyer, Sergej Krohmer, Tobias Sperling, Urs Wetzel, Simon Wörner (Karlsruhe Univeristy of Applied Sciences)
Something that is not often seen: A kite used to generate wind power. Nanotec Electronic GmbH & Co. KG supported this project with six SMCI36 and SMCI35 stepper motor controllers.
It was built by eight aspiring industrial engineers from the Baden-Württemberg Cooperative State University in Heidenheim. With their power plant, the engineers won the Baden-Württemberg challenge of the European Satellite Navigation Competition 2011, also known as "Galileo Masters", and were nominated the best team in Europe.